網(wǎng)絡(luò)轉(zhuǎn)載
您的位置: > 行業(yè)知識 > 網(wǎng)絡(luò)轉(zhuǎn)載 > 詳細內(nèi)容>but the flow angle variesfrom zero at北京車間加濕降塵,車間廠房加濕體系 the
Early booster engines typically incorporated conical nozzles to simplify fabrication. Since booster engines perform only at low altitude and are then jettisoned, peak nozzle efficiency has less of an impact on the total mission. The SSME, however, is used from sea level to orbit insertion. Its nominal thrust time is eight minutes for each mission, and efficient use of the propellants is a prime consideration.
With an aerospike nozzle, ambient pressure places a limit on the expansion process and the thrust loss associated with nozzle over-expansion does not materialize. In addition, the benefits of a variable area ratio nozzle are gained without the complexities associated with variable nozzle geometry. Since ambient pressure controls the nozzle expansion, the flow area at the end of the aerospike changes with altitude. A key advantage of an aerospike is that a very high area ratio nozzle, which provides high vacuum performance, can also be efficiently operated at sea level.
The third nozzle loss mechanism is due to finite-rate chemical kinetics. Ideally, the engine exhaust gas reaches chemical equilibrium at any point in the nozzle flow field, instantaneously adjusting to each new temperature and pressure condition. In real terms, however, the rapidly accelerating nozzle flow does not permit time for the gas to reach full chemical equilibrium. The chemical kinetics efficiency is calculated by comparing the one-dimensional kinetics (ODK) solution to the ODE solution, or:
Given the nozzle area ratio, which, for an aerospike, is a function of engine chamber pressure, required thrust level and vehicle diameter, an ideal "spike" contour can be designed by starting with the known 1-D exit Mach number - which is a function of area ratio - and performing a "reverse expansion" back to the nozzle throat (Mach number=1). The resulting ideal spike contour yields parallel, uniform exit flow, but is, however, excessively long. Since wall pressures and projected nozzle area are minimal toward the end of the "spike," significant length can be eliminated before the loss in thrust becomes excessive. For example, the length of an ideal spike is about 150 percent of a 15 cone. Weight versus nozzle performance trades typically re- duce the nozzle length to the 20 percent range.
The reason for these wall pressure oscillations is found by inspection of a MOC flow field analysis. The expansion at the cowl-lip proceeds until the flow reaches ambient pressure, creating a series of expansion waves that propagate downstream toward the nozzle wall. At the point where the last expansion wave in the series intersects the wall, the wall pressure is near the ambient value. Further expansion is not possible, but the supersonic exhaust gas continues to be gradually turned parallel to the nozzle axis by the contour. This results in a compressive turning region on the nozzle where the wall pressure rises and eventually exceeds the ambient pressure, in some cases by a considerable amount. The resulting compression waves propagate outward toward the constant pressure plume boundary that is established between the engine exhaust gas and the vehicle slipstream.
The first choice for an SSME nozzle contour would obviously be one that maximized nozzle thrust; that is, a Rao optimum contour. However, if a Rao optimum contour was used, the wall pressure at the nozzle exit, (pw(exit)) would be much lower than the ambient pressure at sea level. Even at 100 percent power levels, corresponding to a chamber pressure equal to 3,000 psia, (pw(exit)) would be 4.6 psia or 31 percent of the ambient pressure at sea level. Past experience showed that nozzle flow separation would likely occur if the wall pressure approached this level. Since nozzle flow separation is dependent upon a number of variables (boundary-layer thickness, pressure gradient, Mach number, etc.) and is thus difficult to accurately predict, additional margin in exit pressure was sought. Some margin was also required to permit sea-level testing of engine throttling capability.
Truncation of the full length "spike" results in the formation of a nozzle base region and a performance loss. However, the thrust pro duced by the discarded portion of the spike is not entirely lost. At high altitude, the nozzle flow at the end of the truncated nozzle turns into the base and surrounds a "bubble" of recirculating subsonic flow. Since the wake is closed, no external or ambient influence can be exerted. The important result is that a pressure exists on the nozzle base that partially offsets the truncation loss. Data generated from a variety of cold-flow aerospike tests revealed that the base thrust is a fixed percentage of the thrust generated by the discarded portion of the spike. Knowing the base area (Ab), an average base pressure (Pb) is thus empirically determined for the closed wake case.
The SSME nozzle configuration was the result of a number of design iterations. Various system studies and mission optimizations showed that high nozzle area ratio was critical and the nozzle was configured with an area ratio of 77.5:1, and a length equal to 80 percent of a 15 conical nozzle. The task left to the nozzle designers was to specify the shape of the nozzle contour from the throat to the nozzle end point which was dictated by the area ratio and nozzle length.
本頁關(guān)鍵詞:nozzle,Design,
上一篇: MA 01301 USA 北京車間加濕降塵,車間廠房加濕體系Phone: (413) 772-0846 下一篇: tanker truck or a北京車間加濕降塵,車間廠房加濕體系ny other container to cle
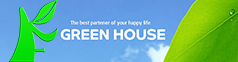