網(wǎng)絡(luò)轉(zhuǎn)載
您的位置: > 行業(yè)知識 > 網(wǎng)絡(luò)轉(zhuǎn)載 > 詳細(xì)內(nèi)容>but the flow angle variesfrom zero at北京車間加濕降塵,車間廠房加濕體系 the(4)
These compression waves reflect from the plume boundary in the form of a series of expansion waves that eventually intersect the nozzle wall downstream of the compression zone. The expansion waves then begin to relieve the high pressure on the wall and a zone of low pressure is thus created downstream of the compression zone. The minimum pressure experienced in this low- pressure zone is typically less than the ambient pressure. When the last expansion wave in the series intersects the nozzle wall, the wall pressure begins to rise again due to the gradual turning caused by the nozzle contour. The process then repeats itself, setting up an alternating series of high- and low-pressure zones on the nozzle wall. Since the average wall pressure is typically greater than the ambient pressure, the flow is not over-expanded.
Experience tells the nozzle designer that a long nozzle is needed to maximize the geometric efficiency; but at the same time, nozzle drag is reduced if the nozzle is shortened. If chemical kinetics are an issue, then the acceleration of exhaust gases at the nozzle throat should be slowed by increasing the radius of curvature applied to the design of the throat region. The optimum nozzle contour is a design compromise that results in a maximum overall nozzle efficiency.
The most basic contour that can be considered for a nozzle is a truncated cone. Conical nozzles yield nearly uniform exit velocity, but the flow angle varies from zero at the axis to the cone half-angle at the wall. Consequently, flow divergence is introduced, which can be expressed as:
High base pressure is, of course, desirable. One common method used for increasing base pressure is the introduction of a secondary gas into the base region. It was found that by injecting secondary flow equal to about one percent of the primary engine flow, engine performance would be optimized. Use of secondary flow in the base also elongates the separation bubble, thereby forming an "aero-dynamic" contour that resembles the truncated portion of the spike. This aerodynamic spike, formed by use of secondary base flow, is the basis for the term "aerospike."
The drag force is obtained by calculation of the momentum deficit in the wall boundary layer. The predicted value for the SSME is 0.986 (1.4 percent loss due to viscous drag).
At the nozzle pressure ratio (NPR - chamber pressure divided by ambient pressure) where the exit flow of an ideal aerospike is at a uniform velocity and at a constant plume diameter (equal to the engine "cowl-lip" diameter), the engine is said to be operating at the "design" condition. At low NPR or low altitude operation, the high ambient pressure "squeezes" the exhaust plume inward toward the nozzle wall. As a result, low altitude operation is characterized by the appearance of a series of alternating pressure peaks and valleys along the nozzle surface.
A Rao design resulted in a wall angle of 7.5 at the nozzle exit. By reducing this angle, additional flow turning is produced, and then, an increase in nozzle wall pressure is created. A study was performed by Rocketdyne engineers in which a large number of parabolic-shaped contours, with a variety of different initial wall angles (qmax) and exit wall angles (qe), were analyzed. After careful analysis of these contours, it was determined that a parabolic contour with qmax=37 and qe=5.3 would produce the desired wall pressure increase with the least amount of performance loss. The wall exit pressure was raised 24 percent (from 4.6 psia to 5.7 psia) at a cost of only 0.1 percent in nozzle efficiency. Validation of the design approach was provided by subsequent testing of the SSME which demonstrated that the engine can be throttled to below 80 percent power level at sea level without nozzle flow separation.
Optimum nozzle configuration for a particular mission depends upon system trades involving performance, thermal issues, weight, fabrication, vehicle integration and cost.
Because the SSME is designed to operate at high chamber pressure (roughly 3,000 psia) and the chemical reactions involving hydrogen and oxygen are not complex, the chemical reaction rates in the SSME are extremely fast; conse- quently, the SSME kinetic efficiency is high:
Nozzle contours can also be designed for reasons other than for maximum thrust. For example, contours can be tailored to yield certain desired pressures or pressure gradients to minimize flow separation concerns at sea level. Rocketdyne has a parabolic curve-fit program, generally used to approximate Rao optimum contours, which can also be used to generate desired nozzle wall pressures.
It had long been assumed that for a given nozzle area ratio and length, there existed a unique nozzle contour that would yield the maximum geometric nozzle efficiency or maximum thrust. In the late 1950s, Dr. G.V.R. Rao derived a method for analytically defining this unique contour. His method is widely accepted by the propulsion industry, and any nozzle contour designed for maximum thrust for a given nozzle area ratio and length is referred to as a Rao optimum contour. By shaping the nozzle wall according to Rao's method, a shorter nozzle and an improvement of over one percent in nozzle efficiency can be obtained relative to a 15 cone.
,噴霧降塵系統(tǒng) ,噴霧降溫設(shè)備 設(shè)計(jì)單位:北京科豐佳華科技有限公司 咨詢熱線:1352-1969-577、1500-1200-355 官方Q Q:820800938 電子郵箱:techkf@qq.com 版權(quán)聲明: but the flow angle variesfrom zero at北京車間加濕降塵,車間廠房加濕體系 the(4)上所有內(nèi)容均有版權(quán)限制,轉(zhuǎn)載請注明出處。 本文地址:http://xelbxh.com/nozzle_spray/nozzlesprayseo20131211570.html本頁關(guān)鍵詞:nozzle,Design,
上一篇: MA 01301 USA 北京車間加濕降塵,車間廠房加濕體系Phone: (413) 772-0846 下一篇: tanker truck or a北京車間加濕降塵,車間廠房加濕體系ny other container to cle
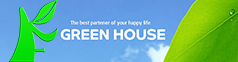