網(wǎng)絡(luò)轉(zhuǎn)載
您的位置: > 行業(yè)知識(shí) > 網(wǎng)絡(luò)轉(zhuǎn)載 > 詳細(xì)內(nèi)容>but the flow angle variesfrom zero at北京車間加濕降塵,車間廠房加濕體系 the(3)
The SSME nozzle is 10.3 inches in diameter at the throat, increasing to 90.7 inches at the nozzle exit over a length of 121 inches. At 100 percent power level, propellants flow through the nozzle at a rate of 1,035 pounds per second. The nozzle accelerates the combustion products to 17,000 feet per second at the nozzle exit, generating 470,000 pounds of thrust at vacuum. Because the last one percent of SSME thrust at a fixed mass flow rate translates to about 5,000 pounds of shuttle payload, high priority was placed on nozzle design and performance.
By allowing the influence of ambient pressure to be transmitted to the nozzle wall, the aerospike yields a net thrust advantage over conventional bell-type nozzles.
The altitude compensating feature of the aerospike results from exposure of the nozzle expansion process to the effect of ambient pressure. High ambient pressure limits expansion at the cowl-lip and prevents the flow from becoming highly over-expanded at sea level. In a high-area-ratio bell nozzle the flow can over-expand to the point where the flow separates from the nozzle wall, producing undesirable lateral forces. As the ambient pressure decreases with increasing altitude, the nozzle exhausts for both the aerospike and the bell nozzle are capable of greater expansion.
Since more of the SSME operation is at high rather than low altitude, vacuum performance is the overriding factor relating to mission performance and high nozzle area ratio is therefore desirable. However, nozzle over-expansion at sea level does result in a thrust loss because the wall pressure near the nozzle exit is below ambient pressure. If the nozzle exit area could somehow be reduced for launch and then gradually increased during ascent, overall mission performance would be improved. The ideal rocket engine would make use of a continuously changing "rubber" or variable-geometry nozzle that adjusted contour, area ratio and length to match the varying altitude conditions encountered during ascent. This feature is referred to as altitude compensation.
For single-stage-to-orbit (SSTO) applications, where performance margins are even more stringent than for the SSME, some form of altitude compensation in the nozzle is a must. An SSTO vehicle relies on a single propulsion system that operates from sea level to orbit. The aerospike engine, built and tested by Rocketdyne in the 1960s, is currently being evaluated for potential use with an SSTO vehicle because of its built-in altitude compensation features and the beneficial manner in which it "packages" or integrates with the vehicle.
There are several classes of bell-type nozzles from which to choose. A nozzle contour designed to produce parallel, uniform exit flow, thereby yielding 100 percent geometric nozzle efficiency, is called an ideal nozzle. But this ideal nozzle is extremely long and the high viscous drag and nozzle weight that result are unacceptable. Some design approaches consider truncating ideal nozzles until the weight considerations, hgeo and hdrag are optimized.
本頁(yè)關(guān)鍵詞:nozzle,Design,
上一篇: MA 01301 USA 北京車間加濕降塵,車間廠房加濕體系Phone: (413) 772-0846 下一篇: tanker truck or a北京車間加濕降塵,車間廠房加濕體系ny other container to cle
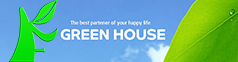